What does TCP offer with Epicor Kinetic?
Epicor Kinetic Solutions
Epicor® meets the needs of the plastics industry, which is challenged to adapt quickly to the development of new products and which requires agility within the organization. All types of plastic industries (including those handling extrusion, injection, molding, thermoforming, plastic bag and film manufacturing) can: Strengthen delivery scheduling Reduce excess inventories Better manage raw materials Increasing profitability
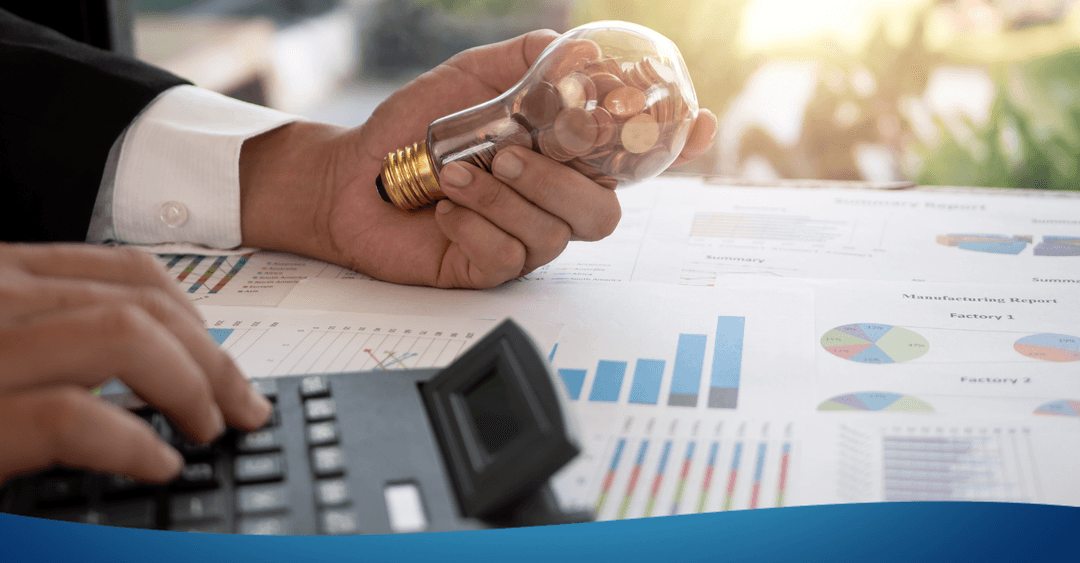
Management of Production Costs
Manage detailed costs of each production run in real time. Compare actual data with estimates, track labor costs, material loading, subcontracting, operations (labor and freight). Production cost can be tracked by job order, by customer, by part or product group, or at the overall company level.
- Track real-time production run costs
- Compare actuals to job estimates
- Monitor labor and material usage
- Capture subcontracting and freight expenses
- Analyze costs by part group
- Break down costs by customer
- Control company-wide cost visibility
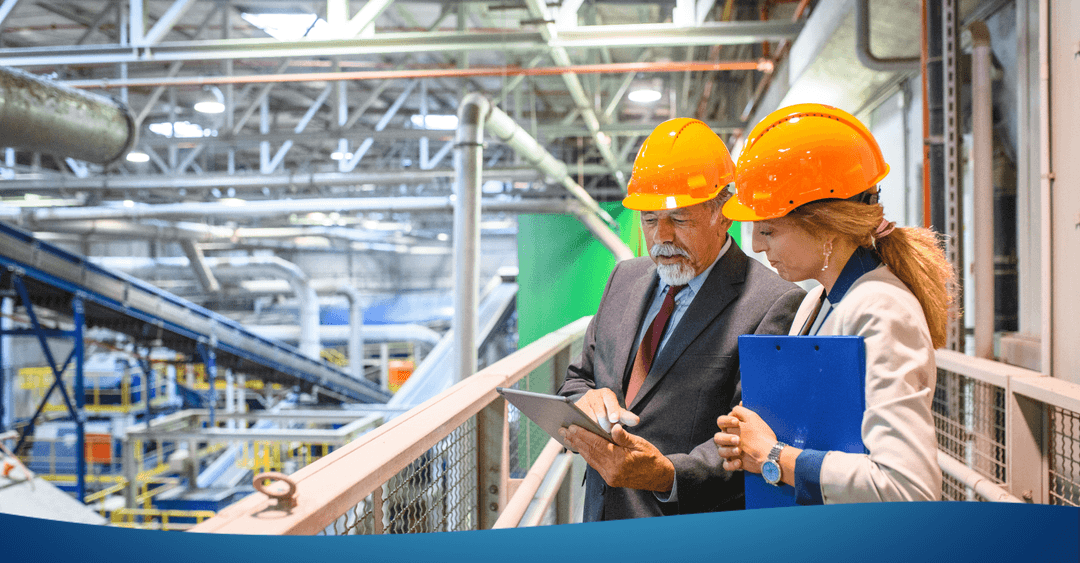
Quality Management
The Quality Suite provides a comprehensive approach to automate processes in compliance with ISO/AS/TS standards.
- Automate quality checks and documentation
- Ensure ISO/AS/TS standards compliance
- Track inspections throughout production runs
- Manage nonconformance and corrective actions
- Standardize processes across all shifts
- Audit-ready records and traceability tools
- Integrate quality with shop floor
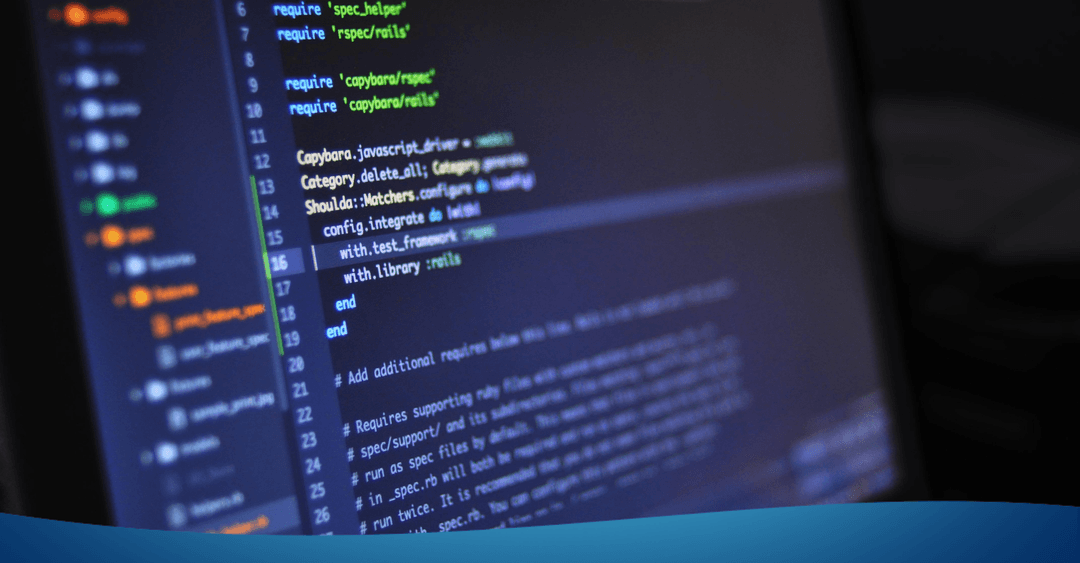
Advanced Programming
Advanced programming to optimally and efficiently meet customer requirements.
- Optimize programs for customer specifications
- Automate setups for faster production
- Reduce downtime with intelligent scheduling
- Support complex mold and tooling configurations
- Customize workflows for unique orders
- Adapt quickly to design changes
- Maximize efficiency with smart automation
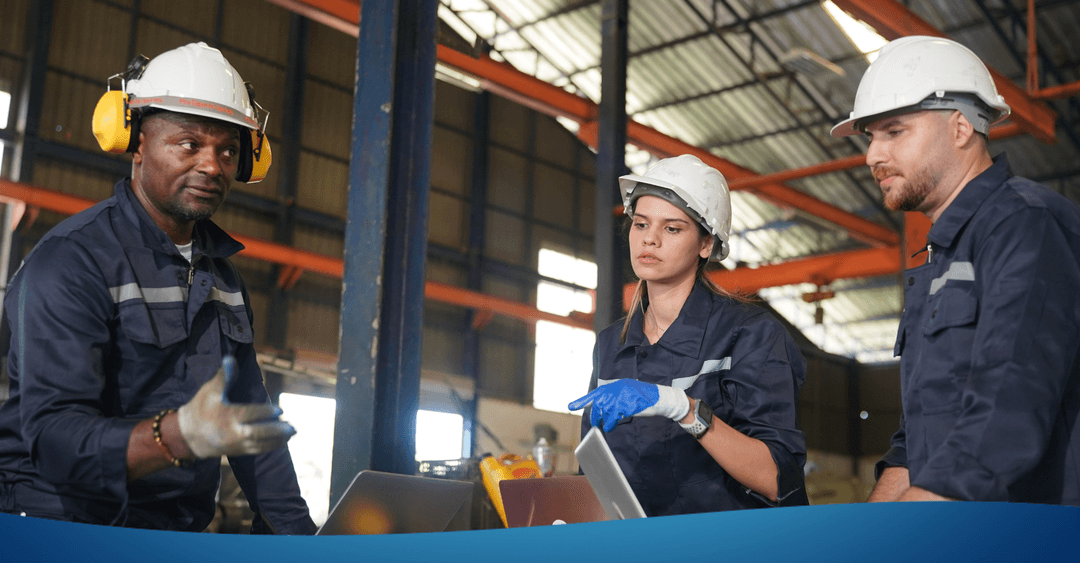
Production Planning
The integration of production planning and scheduling allows you to respond quickly to changing customer demands in a flexible and accurate manner. This way your company will have an efficient and profitable operation.
- Respond quickly to customer changes
- Integrate planning with real-time data
- Improve accuracy in job scheduling
- Maximize machine and labor utilization
- Adapt schedules with minimal disruption
- Reduce lead times and bottlenecks
- Boost efficiency and profitability consistently
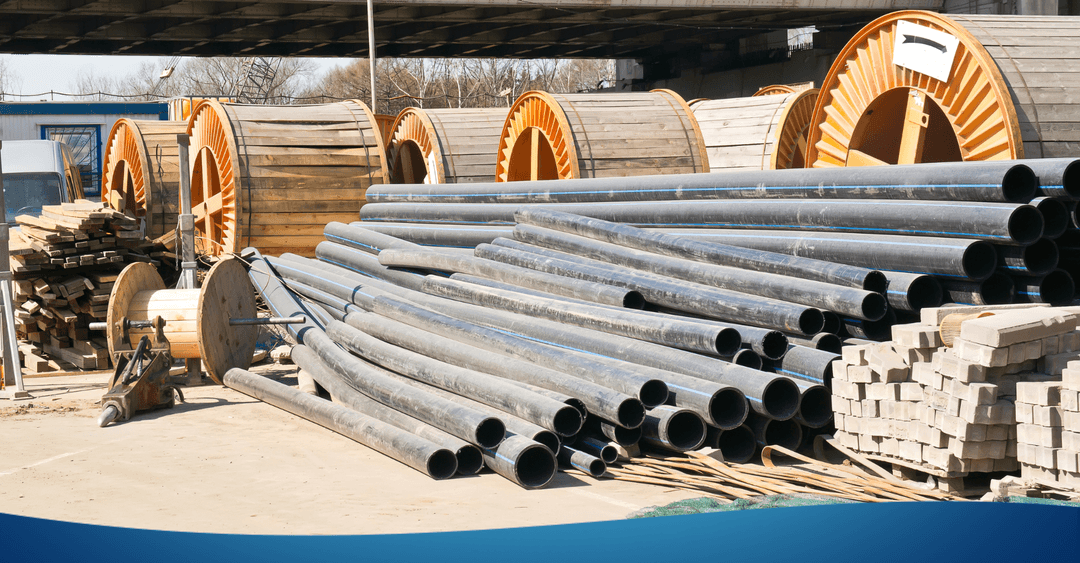
Material Requirements
MRP to manage the planning of purchases of a wide variety of inputs, adjust production as sales forecasts change, and cover shortages in raw material inventories in advance.
- Plan purchases across material types
- Adjust production to forecast changes
- Anticipate and prevent material shortages
- Automate purchasing based on demand
- Balance inventory with real-time needs
- Synchronize supply with production schedules
- Improve planning accuracy and efficiency